Total Productive Maintenance (TPM) é uma metodologia que busca maximizar a eficiência dos equipamentos por meio do envolvimento de todos os funcionários.
Tem foco na manutenção preventiva, na melhoria contínua e na participação dos operadores para eliminar falhas, reduzir paradas não planejadas e aumentar a produtividade.
Como veremos neste conteúdo, ela estabelece um regime em que todos são responsáveis pelo bom funcionamento das máquinas e equipamentos de produção.
Entenda como funciona, seus benefícios e muito mais.
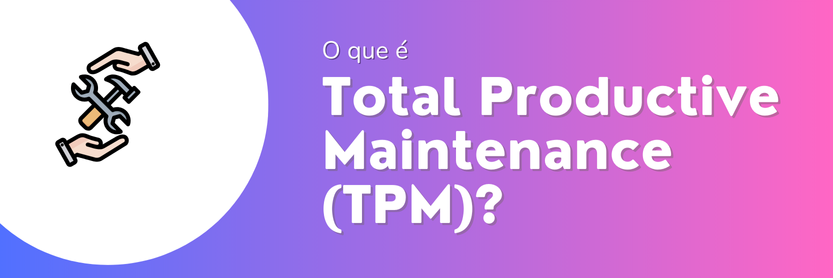
O que é Total Productive Maintenance (TPM)?
Total Productive Maintenance (TPM) é uma metodologia de gestão que busca maximizar a eficiência dos equipamentos através do envolvimento de todos os funcionários.
Seu objetivo é reduzir falhas, paradas não planejadas e defeitos, aumentando a produtividade e a qualidade.
A TPM promove uma cultura de responsabilidade compartilhada pela manutenção e desempenho dos equipamentos, contribuindo para operações mais eficientes e competitivas.
Tem como base um conjunto de oito princípios ou pilares que sustentam as iniciativas.
Quanto mais mecanizada ou dependente de máquinas uma empresa for, mais necessária a TPM será.
Nas indústrias que operam em um regime 24/7, ela é indispensável para garantir que a produção em série não seja interrompida.
Quais os benefícios do Total Productive Maintenance?
A maior vantagem de aderir à metodologia TPM é dar mais segurança para que uma produção continue sem parar.
Entre os benefícios diretos que ela proporciona, destacamos:
- Aumento da eficiência operacional
- Redução de paradas não programadas
- Melhoria na qualidade dos produtos
- Aumento da vida útil dos equipamentos
- Maior envolvimento dos colaboradores
- Diminuição de custos de manutenção
- Aumento da segurança no ambiente de trabalho
- Maior produtividade e lucratividade.
8 pilares do Total Productive Maintenance
A Manutenção Produtiva Total só se estabelece em empresas que sigam os oito princípios que servem como guia para orientar as decisões dos colaboradores.
Veja na sequência que princípios são esses e como eles podem fazer a diferença entre uma linha de produção efetiva de ponta a ponta.
1. Manutenção autônoma
Tarefas simples como limpeza, lubrificação e pequenos reparos podem ser realizadas pelos próprios operadores das máquinas e equipamentos industriais.
É nisso que consiste o princípio mais importante da TPM, o de manutenção autônoma, em que cada um é responsável pelas suas rotinas básicas.
2. Manutenção planejada
Em certos casos, é preciso não só limpar e ajustar, mas programar manutenções regulares e preventivas, visando minimizar paradas inesperadas e prolongar a vida útil dos equipamentos.
Ainda que essas rotinas possam ser realizadas por especialistas, o ideal é que elas também sejam executadas pelos próprios operadores que utilizam as máquinas no dia a dia.
3. Melhoria focada
A TPM defende sobretudo a proatividade.
Por isso, o princípio da melhoria focada estabelece que cada um pode e deve se responsabilizar pela “fiscalização” dos equipamentos usados na produção.
Em vez de esperar alguém fazer esse trabalho, cada operário atua em prol da melhoria contínua, identificando e reportando possíveis ações nesse sentido.
4. Treinamento e desenvolvimento
Não pode haver TPM sem um corpo de profissionais qualificado.
Dessa forma, toda empresa que pretende se orientar por esse modelo de manutenção precisa seguir o princípio do treinamento e desenvolvimento de pessoas.
5. Manutenção de qualidade
Uma máquina que para constantemente ou que dá defeitos recorrentes certamente deixa a desejar em termos de qualidade.
O princípio da qualidade, nesse caso, orienta a gestão a dispor de equipamentos dentro de certo padrão.
Assim, ela evita não apenas os defeitos, como garante que os produtos fabricados atendam às expectativas do consumidor.
6. Segurança e meio ambiente
Embora o foco na TPM sejam as máquinas e equipamentos, não se pode jamais descuidar do fator humano.
Dessa forma, é preciso seguir à risca o princípio do cuidado com a segurança do trabalho e com os impactos gerados sobre o meio ambiente.
7. Gestão de equipamentos
A operação de máquinas em regime industrial gera dados que podem ser usados para medir suas performances.
Também podem servir como parâmetro para melhorias e para identificar com antecedência eventuais falhas.
8. Manutenção baseada em dados
Os dados gerados formarão com o tempo um repositório que, no futuro, pode ser usado como referência para a tomada de decisão em questões envolvendo a manutenção preditiva e para garantir a melhor performance dos equipamentos.
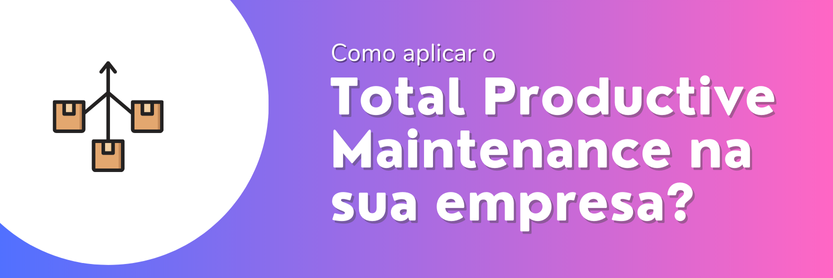
Como aplicar o Total Productive Maintenance na sua empresa?
Para aplicar o TPM na sua empresa, siga estas dicas:
- Envolva todos os funcionários: promova a participação ativa de toda a equipe
- Implementação da manutenção autônoma: capacite operadores a realizar manutenção básica
- Manutenção preventiva: estabeleça rotinas para evitar falhas nos equipamentos
- Educação e treinamento: ofereça capacitação contínua em práticas de TPM
- Melhoria contínua: utilize indicadores de desempenho para identificar e eliminar perdas
- Forme equipes multifuncionais: reúna diferentes áreas para solucionar problemas
- Padronização de processos: crie procedimentos claros para operações e manutenção.
A Escola EDTI capacita os líderes das grandes empresas brasileiras há mais de 15 anos.
Nossos cursos EAD e de formação Green Belt e Black Belt são para você, que quer mergulhar fundo na metodologia Lean Six Sigma.
Venha para a EDTI e entre no mercado com um certificado de formação reconhecido pela The Council for Six Sigma Certification!
Conclusão
Total Productive Maintenance é a base que serve como referência para pautar as decisões envolvendo a manutenção em empresas de todos os portes.
Agora que você sabe como ela funciona, pode ser que queira ir mais longe e ampliar seus conhecimentos sobre esse tópico.