A manutenção detectiva, muitas vezes, é a única forma de descobrir a origem de um problema em máquinas e equipamentos.
Como o nome já indica, trata-se de um tipo de serviço em que se busca detectar algo, como fazem os médicos ao realizarem testes e exames ambulatoriais ou de laboratório.
Para a indústria, sua importância é semelhante.
Afinal, uma manutenção detectiva bem feita representa uma maneira segura de diagnosticar o que está por trás de um defeito ou mau funcionamento.
Avance na leitura e entenda como funciona, em que casos se aplica e quais os tipos de manutenção detectiva mais utilizados.
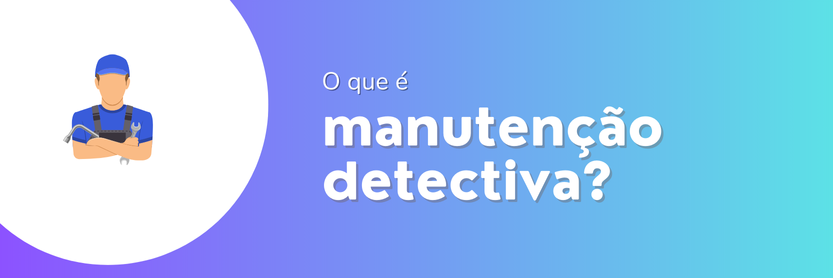
O que é manutenção detectiva?
Manutenção detectiva é a abordagem com a qual se investiga a origem de eventuais defeitos, desvios ou falhas em máquinas e equipamentos, principalmente industriais.
Para isso, utilizam-se diversos aparelhos, medidores e outros instrumentos para medir parâmetros, de modo que se possa descobrir onde pode estar um problema.
Ela acompanha muitas das vezes as rotinas de manutenção preventiva, cuja finalidade é antecipar-se aos defeitos por meio de ações de prevenção de falhas.
Qual a diferença entre manutenção preditiva e detectiva?
Se você acompanha o blog da EDTI, provavelmente já leu sobre manutenção em suas modalidades preventiva, corretiva e preditiva, além da TPM e RCM.
A preditiva pode ser facilmente confundida com a manutenção detectiva, considerando que ela também visa encontrar possíveis focos de defeitos.
A diferença entre essas duas modalidades está na forma com que lidam com os dados levantados.
Enquanto a manutenção preditiva coleta dados para que se possa decidir o que fazer, na detectiva, os dados já existem, cabendo aos profissionais de manutenção confirmá-los ou não.
Os exemplos a seguir vão ajudar a entender melhor.
Exemplos de manutenção detectiva
Assim como um médico se vale de uma extensa bateria de exames e testes para detectar anormalidades, o mesmo acontece com quem trabalha em manutenção detectiva.
Para que ela possa ser feita, são empregados uma série de dispositivos, equipamentos e sensores, cada um apto a detectar anomalias nos parâmetros aferidos.
Conheça na sequência seis deles, como funcionam e para que servem.
Análise de vibração
Alguns tipos de motor operam em condições que, se forem extrapoladas, podem fazer com que sejam exigidos acima de suas capacidades.
Quando isso acontece, é possível que eles vibrem ou apresentem tremores fora do espectro aceitável.
Nesses casos, o uso de sensores em análises de vibração é indicado para detectar vibrações anormais em motores, rolamentos e máquinas em geral.
Termografia
A temperatura é outro parâmetro que, quando foge de certa faixa, representa um mau indicador.
Os carros são um bom exemplo disso, já que só funcionam normalmente entre 87°C e 105°C.
Os equipamentos industriais seguem a mesma lógica.
Por isso, todo aumento de temperatura é medido com aparelhos de termografia para identificar focos de superaquecimento, como pode ocorrer com painéis elétricos e equipamentos mecânicos.
Análise de óleo lubrificante
A função dos óleos lubrificantes é garantir que as peças, engrenagens e componentes de motores, em especial à combustão, movam-se sem atrito, evitando o desgaste prematuro.
Os fluidos devem apresentar certa consistência, não devendo ser nem muito “aguados”, nem muito espessos.
Também devem ser livres de partículas sólidas que possam penetrar nos motores ou causar mau funcionamento.
Dessa forma, são feitos testes e inspeções do óleo para verificar a presença de partículas metálicas ou contaminação.
Teste de ultrassom
Certos tipos de equipamento estão sujeitos a vazamentos de gases ou de ar em razão da sua forma de funcionamento.
Um trocador de calor, por exemplo, pode ser testado com teste de ultrassom para detectar vazamentos internos nos tubos, garantindo a eficiência térmica do equipamento e prevenindo falhas operacionais.
Esse é o exame indicado para a detecção de vazamentos de ar comprimido ou gases por meio de sensores ultrassônicos, bastante utilizado em escala industrial.
Inspeção com endoscópio industrial
Algumas instalações industriais são equipadas com extensas tubulações, algumas em lugares de difícil acesso ou no subterrâneo.
Quando se faz necessário inspecioná-las, o endoscópio industrial é o dispositivo mais indicado.
Com ele, utilizam-se pequenas câmeras que são introduzidas por cabos, permitindo examinar o interior de tubulações e motores sem desmontá-los.
Monitoramento de corrente elétrica
Para certos tipos de equipamento, a medição do consumo elétrico é o meio de identificar sobrecargas ou falhas.
Assim são os compressores de ar que podem ser testados com monitoramento de corrente elétrica para detectar desequilíbrios, sobrecarga ou falhas nos componentes elétricos, como o motor ou o inversor de frequência.
Qual a importância da manutenção detectiva?
Como vimos até aqui, existem certos parâmetros a serem mantidos para garantir o bom funcionamento de um motor, equipamento ou máquina.
A manutenção detectiva é fundamental nesse sentido porque tem como principal finalidade assegurar que esses parâmetros estão sendo observados ou não.
A falta desse tipo de manutenção já é um problema, por sinalizar que a empresa opera seus equipamentos sem parâmetros seguros.
Sem conhecer seus limites, o risco de falhas, desvios e acidentes aumenta, prejudicando com isso a própria continuidade das atividades.
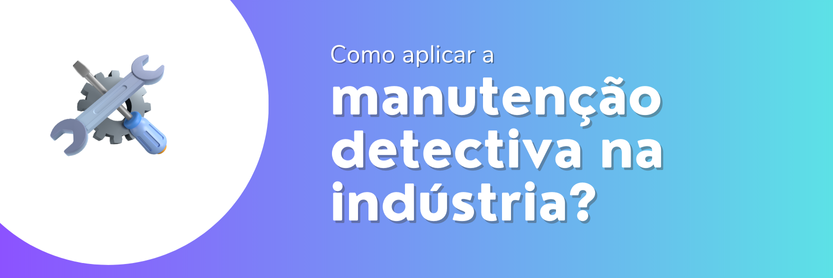
Como aplicar a manutenção detectiva na indústria?
A manutenção detectiva pode ser implementada com o apoio de profissionais especializados, seguindo os seguintes passos:
- Implementando monitoramento contínuo: com o uso de sensores e sistemas automatizados para coletar dados em tempo real, como vibração, temperatura e pressão
- Realizando análises periódicas: fazendo inspeções com ferramentas como termografia, ultrassom e análise de óleo, verificando condições antes das falhas ocorrerem
- Capacitando a equipe: treinando operadores e técnicos para interpretar dados e identificar sinais de falhas potenciais
- Planejando manutenções programadas: agendando verificações regulares, baseadas em históricos de desempenho e previsões de falhas
- Aplicando IA e Big Data: utilizando tecnologias avançadas para prever falhas e otimizar o processo de manutenção.
Conclusão
A manutenção detectiva é para profissionais.
No segmento industrial, ela é de grande importância para a detecção de problemas e para se chegar à causa raiz de uma falha.
Está ao seu alcance ser o especialista que dá às empresas as respostas aos seus desafios.
Capacite-se nos cursos EAD, Green Belt e Black Belt em Lean Six Sigma da Escola EDTI e faça a diferença.