Você certamente já mediu sua própria capacidade produtiva em algum momento, nem que seja de cabeça.
Sem conhecer as próprias capacidades, seria quase impossível conseguir um emprego.
Os concursos públicos são um bom exemplo disso, afinal, para obter a aprovação, precisamos saber quantas questões somos capazes de responder corretamente em uma prova.
Em segmentos como o industrial, então, nem se fala.
Medir o quanto se pode produzir não é só uma questão de organização, mas de sobrevivência.
Por essa razão, neste texto, vamos jogar uma lente de aumento sobre esse tema de fundamental importância, destacando como a metodologia Lean Six Sigma pode ajudar.
Prossiga a leitura até o final!
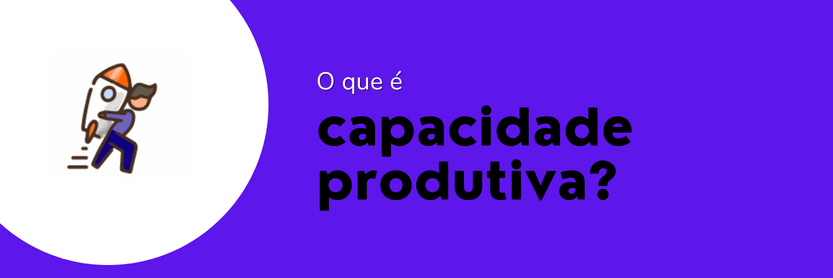
O que é capacidade produtiva?
Capacidade produtiva pode ser definida como uma equação que calcula o quanto se pode produzir em um certo período de tempo com uma certa quantidade de recursos.
Para a indústria, conhecer a capacidade de produção faz toda a diferença, já que esse é um fator de competitividade.
Significa que, se um concorrente produz X e sua empresa produzir X-1, ela estará em desvantagem, já que não consegue atender a mesma demanda.
Porém, aumentar a capacidade produtiva apenas por aumentar não é sinônimo de sucesso.
Mais do que isso, é preciso otimizar essa capacidade, e fazer isso de forma racional.
Por que medir a capacidade produtiva?
Quando nos habilitamos a antecipar o quanto somos capazes de produzir, ganhamos uma vantagem considerável.
Primeiramente porque, com essa informação estratégica, poderemos antecipar os custos de produção e, assim, definir o quanto precisaremos obter de lucro para arcar com esses custos.
Calcular a capacidade de produção é também uma maneira de saber das reais forças de uma empresa, como previsto na análise SWOT.
Sabendo do que somos capazes, podemos definir objetivos ousados e ao mesmo tempo realistas, considerando os contextos interno e externo.
Como medir a capacidade produtiva de uma empresa?
O cálculo real da capacidade produtiva é dividido em três partes: a capacidade instalada, a efetiva e a realizada.
A capacidade instalada mede quantas horas uma indústria é capaz de produzir.
Por exemplo, uma linha de montagem que tenha 40 máquinas operadas por 8 horas diárias tem uma capacidade de operar por 320 horas por dia.
Agora, é preciso saber quantas unidades a empresa consegue produzir em um dia.
Imagine então que uma fábrica de sucos produz uma garrafa em 12 minutos, o que equivale a 0,2 hora.
Nesse caso, 320 / 0,2 = 1,6 mil garrafas por dia.
Essa é a capacidade instalada.
Com esses dados, podemos enfim calcular a capacidade efetiva, para a qual precisamos estimar as perdas diárias.
Suponha, nesse caso, que a linha de produção tem perdas de 2% (32) por dia, o que diminuiria esse número para 1.568 garrafas de suco produzidas.
Finalmente, para saber a capacidade realizada, é necessário considerar perdas imprevistas, como máquinas paradas ou falta de insumos.
Imagine então que a empresa tem perdas diárias desse tipo de 3% (48).
Dessa forma, a capacidade realizada passaria para 1.520 garrafas por dia.
Como calcular a capacidade produtiva de uma máquina?
Para um cálculo ainda mais exato da capacidade de produção, vale também calcular o quanto cada máquina é capaz de produzir.
Uma das ferramentas mais usadas para isso é o cálculo conhecido como Overall Equipment Effectiveness (OEE), cuja finalidade é medir a eficiência global de um equipamento.
Sua fórmula é a seguinte:
- OEE (%) = disponibilidade x performance x qualidade
Veja abaixo como calcular cada um dos três itens:
- Disponibilidade = tempo da máquina em atividade / tempo de produção planejado
- Performance = (unidades produzidas / tempo em atividade) / tempo ideal de atividade
- Qualidade = unidades em conformidade / total de unidades produzidas.
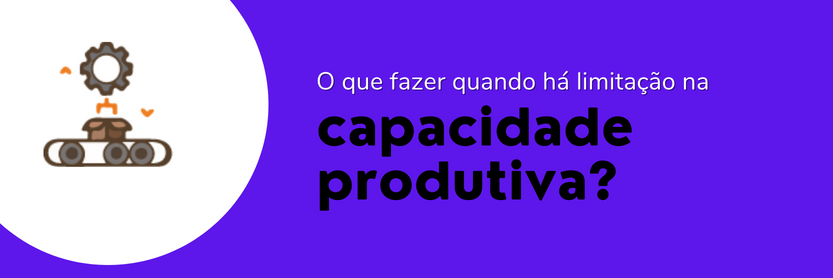
O que fazer quando há limitação na capacidade produtiva?
A imensa maioria das indústrias trabalha com linhas de produto variadas.
Assim, é esperado que, para alguns desses produtos, a capacidade seja maior, e para outros, ela diminua.
O que fazer, então, para não ficar “entre a cruz e a espada”, sem saber qual deles deve ter sua produção priorizada?
Uma maneira de fazer isso é utilizar a Matriz BCG, ferramenta sobre a qual já falamos aqui no blog da EDTI.
Consiste em elencar os produtos em quatro quadrantes, nos quais o eixo vertical determina o potencial de crescimento e o vertical a participação no mercado.
Dessa forma, os produtos são classificados em 4 categorias:
- Estrela: produtos com alto potencial de crescimento e alta participação
- Vaca leiteira: produtos com baixo potencial de crescimento e alta participação
- Abacaxi: produtos com baixo potencial de crescimento e baixa participação
- Interrogação: produtos com potencial de crescimento, mas baixa participação.
Uma vez que você saiba quais os produtos apresentam maior potencial de participação, poderá então decidir quais deles deverá priorizar quando sua capacidade for limitada.
Como aumentar a capacidade produtiva de uma empresa
Após calcular a sua capacidade produtiva, existem três alternativas.
Uma é o cálculo revelar que a produção está no máximo da capacidade.
Outra é quando a produção está em níveis aceitáveis, embora abaixo do máximo, e na terceira, a produção está abaixo dos parâmetros considerados ideais.
Se os seus resultados se enquadram no terceiro caso, então será necessário adotar algumas medidas para retomar a capacidade produtiva.
Veja a seguir.
👉 A Inteligência Artificial também pode ajudar a sua empresa a produzir mais. Confira neste e-book!
Modele os processos
O Business Process Modeling (BPM) é o conjunto de etapas previstas no Guia para o Gerenciamento de Processos de Negócio – ABPMP BPM CBOK V3.0. para aprimoramento de um processo.
Como mostramos neste artigo sobre modelagem de processos, ela pode ser feita em sete etapas:
Etapa 1 – Formar equipes que possam identificar uma rotina
Etapa 2 – Identificar os processos envolvidos
Etapa 3 – Identificar os processos atuais
Etapa 4 – Fazer a análise do processo e propor melhorias
Etapa 5 – Mapear os chamados “fluxos To Be”
Etapa 6 – Priorizar tarefas e automatizar as que assim exigirem
Etapa 7 – Monitorar resultados, melhorar e expandir automatização.
Crie rotinas de manutenção
A falha humana é uma das principais causas de perdas na indústria, levando a prejuízos diretos e indiretos.
No segundo caso, ela pode ocasionar perda de eficiência em máquinas, ao negligenciar sua manutenção e reparos.
Para evitar isso, o ideal é definir rotinas de manutenção, tanto preventivas quanto preditivas, como mostramos neste artigo sobre o plano de manutenção.
Treine os trabalhadores
Considerando a relevância da mão de obra e os riscos da falha humana, tão importante quanto cuidar da manutenção é treinar as pessoas.
Dessa forma, a produtividade tende a aumentar, até porque trabalhadores treinados são normalmente mais motivados e atentos ao que fazem.
Aumente a quantidade de horas de trabalho
Há também a possibilidade de a indústria operar no máximo de suas capacidades diárias.
Uma solução nesse caso é aumentar a quantidade de horas em atividade, sempre observando os custos que isso deve gerar em termos de mão de obra, uso de energia e insumos.
Em certas situações, pode ser até necessária a criação de turnos extras de trabalho, para os quais o ideal é contratar novos trabalhadores.
Invista em automação
Sabemos que a maioria das indústrias hoje conta com processos automatizados de produção.
Por isso, a questão é: será que não dá para avançar mais nesse aspecto?
A robótica tem trazido contribuições incríveis para o segmento industrial, com equipamentos que podem ser operados quase como videogames.
Vale então considerar a capacidade de investimento e, na medida do possível, implementar soluções que aumentem a produtividade a partir da automatização.
Melhore o ambiente de trabalho
Nem só de máquinas vive a indústria.
Afinal, sem pessoas, seria impossível produzir qualquer coisa, já que nem mesmo os robôs mais avançados se operam sozinhos.
Esse é um bom motivo para buscar melhorar o ambiente de trabalho, por meio de iniciativas que tornem o clima organizacional mais estimulante.
Dê incentivos
Falando em estímulo, uma maneira de aumentar a capacidade produtiva sem ter que realizar grandes investimentos em infraestrutura é criar programas de incentivo.
Pode ser uma remuneração extra para trabalhadores que produzirem mais ou outro tipo de prêmios para quem se destacar.
Como a tecnologia pode impulsionar a capacidade produtiva?
A indústria 4.0 é uma realidade e as empresas que não se ajustarem vão ficar para trás.
Nesse aspecto, é preciso contar com profissionais qualificados que deem conta dos muitos desafios dessa que é a etapa mais recente da evolução industrial.
Quem se atualiza acaba tendo as melhores oportunidades, chegando ao ponto de ser disputado pelas empresas.
Você pode alcançar esse patamar com os cursos green belt e black belt da Escola EDTI, que também tem modalidades a distância.
Conclusão
Medir a capacidade produtiva é só o começo quando se trata de atingir objetivos de negócio.
Para alcançar as metas mais ousadas, as empresas precisam de profissionais qualificados, e é aí que você entra.
O curso green belt em Lean Six Sigma da EDTI capacita profissionais há mais de dez anos, com uma formação diferenciada e de alto nível.
Seja um especialista ainda mais completo, baixando este kit de materiais para análise de dados!